In the manufacturing industry, it is our social responsibility to try to minimize our impact on the environment
when we choose materials and use energy to make our products. By fulfilling this responsibility while engaging in
business activities, we will contribute to the realization of a sustainable society.
Our approach to the creation of a recycling-oriented society
Based on a recognition of the fact that all activities of
human civilization, including those of the TOKYO KEIKI
Group, are dependent on coexistence with the natural
environment, the Group is promoting initiatives for the
development of a sustainable, recycling-oriented society.
Specific measures for reducing waste
Compliance with laws and regulations
Waste is disposed of appropriately in accordance with laws
and government ordinances, as well as the regulations of the
municipalities where our factories and plants are located.
Promoting the “3 Rs”
・Reuse
We are now reusing some of our used products and parts
(including electronic parts) with the approval of our customers.
・Reduce
We are engaging in an initiative in which we have introduced
reusable containers with some of our customers and our
partner factories that can be used to move goods between
each other’s factories, eliminating waste such as cardboard
and packaging materials. In addition, the use of equipment
to reclaim wash oil and the evaporation and drying of waste
water from glass processing are helping to reduce the amount
of waste water and waste oil we produce.
In FY 2021, the amount of industrial waste we output
increased due to such factors as increased PCB waste at the
Sano Plant and etchant at the Nasu Plant. Note that figures
from TOKYO KEIKI PRECISION TECHNOLOGY (TPT) are
included from this report forward.
・Recycle
We hire contractors to take our scrap metal, waste oil, and
waste paper, which are valuable recyclable materials, and
accordingly thoroughly separate our waste.
The breakdown for these valuable recyclable materials for
FY 2021 was 469 t of scrap metal, 19 t of waste oil, and 54 t
of waste paper.
Amount of industrial waste produced
Valuable recyclable materials produced
Recycling used wash oil
The Sano Plant alone accounts for approximately two-thirds
of the company’s overall waste output, and roughly half of
that is water-soluble cutting fluid, wash oil, and other types of
waste oil. To date, we have hired contractors to collect all of
this. Having established a goal of reducing waste, however,
we installed equipment in the factories to recycle hydrocarbon
wash oil, making it possible to separate the oil content
from wash oil before disposing of the leftover fluid. This has
enabled us to recycle 90% of waste oil and use it like new
wash oil, contributing to the effective utilization of resources. In
FY 2021, we achieved a reduction in waste oil of 6,686 liters,
double that of FY 2020. Going forward, we will continue to
recycle waste oil to reduce our waste output.
Amount of waste oil reduced through use of wash oil recycling equipment (FY2021)
Initiative to reduce waste from processing defects
Ductile iron is a very strong material used in our high-pressure
hydraulic products, and when drilling small-diameter holes or
tapping this material, tools can sometimes break. In the past, when
this happened, we would discard the entire part being worked on.
Because of this, when such a defect occurred with a large part
just before being completed, not only was there a loss of material;
there was also a significant loss in terms of the energy put into
processing, and it could even lead to delayed product delivery.
Because this issue could not be completely prevented solely
by improving the tools or processing conditions, we installed an
electrical discharge machine at the Sano Plant that enables broken
tools to be removed without damaging the part being worked on.
In the one-year period after installing the machine, approximately
50 parts were able to be saved without discarding them, including
large parts weighing over 30 kilograms. This also enabled savings
in power consumption by processing equipment, which takes
over an hour per part. Going forward, we will continue to promote
initiatives aimed at the effective use of limited resources.
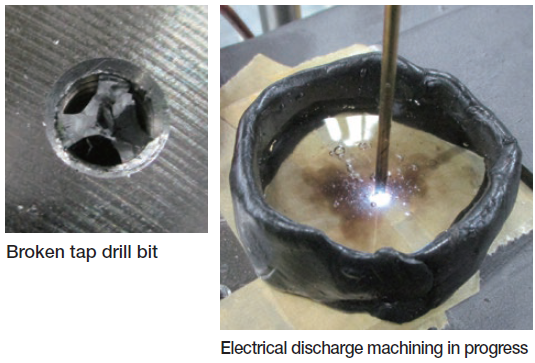
Going paperless with design issuing
In the past, the design section in the Engineering Department
was in charge of issuing design documents used by the
Production Department, printing blueprints and parts lists
before sending them. However, the fact that the printing work
took time as well as that a large amount of paper resources
were consumed for each issue were problems. In order to
improve on these problems, the Engineering & Products
Service Office, which supervises the entire Group, developed
a design issue management tool.
The genres of the products that the Group produces differ
greatly depending on business segment and production
site, and their production flows also differ. Accordingly, it was
thought that development of such a tool would be extremely
difficult. It was determined, however, that swift improvements
were necessary from a sustainability perspective and,
with the help and understanding of a great number of
departments, development moved forward in a short span of
time. The Production Departments provided full cooperation
in the development of the tool. After analyzing the flow of
production, every effort was made to avoid significantly
impacting existing work operations in the perfection of a
generic, all-purpose routine for issuing electronic designs for
products at the Yaita Plant, serving as a first stage for the
development of the tool.
The result was the elimination of an equivalent of 160,000
A4-sized printed pages of paper, as well as an approximate
1,000-hour reduction in the work involved in issuing and
receiving blueprints over a one-year span. There was also an
incidental benefit in terms of a reduction in time spent dealing
with inquiries regarding the progress of designs being issued.
Going forward, these results will be extended to the Nasu
and Sano Plants as we engage in continuous improvements
in work operations and contribute to the conservation of
resources.
A screenshot of the design issue management tool input screen

Specific measures for proper management of chemicals
Policies
Some chemical substances have harmful effects on the
environment and human body. As such, it is companies’
social responsibility to manage them properly and to take the
environment and occupational safety into account. We are
working to cut our emissions of chemicals by setting voluntary
reduction targets.
Switching to alternatives to hazardous chemicals
Each of our factories is actively switching to alternative
materials to hazardous chemicals.
- Cleaning agents for hydraulic products
Switched from dichloromethane to hydrocarbon-based
- Thinners
Switched to alternatives free from toluene and xylene
- Cutting fluid
Switched to alternatives free from chlorine
Green partner initiative
The “Green Partner System” is an initiative to eliminate
hazardous substances from production processes throughout
the supply chain in order to encourage environmentally friendly
manufacturing. TOKYO KEIKI is putting this system into
practice alongside our suppliers, subcontractors, and other
partners.
Under this initiative, partners who meet our management
standards and have the ability to conduct independent quality
management to prevent hazardous substances being used in
or contaminating their production lines are certified as Green
Partners. This eliminates the need to submit a non-inclusion
certificate for each product or part and to conduct some of
the tests on the chemical substances they contain. We also
provide various services to Green Partners, such as support
for the testing and analysis of chemical substances contained
in parts and materials, provision of environment-related
information, and support for environment-related education.
Reducing hazardous waste
We are working to reduce the amount of hazardous
substances that we dispose of by reviewing purchase
lots, reducing excess inventory by subdividing orders, and
encouraging the purchase of products that do not use
hazardous substances.
In the past, we used dichloromethane to remove oil from the surface of hydraulic products produced at the Sano Plant
prior to the coating process. Dichloromethane, however, is
a highly toxic chemical substance. We made the decision to
switch to a less toxic hydrocarbon-based cleaning agent and
designed and built our own dedicated cleaning equipment.
We began using this equipment in January 2021 and
ultimately used 495 kilograms of dichloromethane in FY 2021.
This was a drastic 95% reduction in comparison with FY
2020.
PRTR emissions: Sano Plant *Emissions only (excluding transfers)
FY |
Dichloromethane (kg) |
Toluene (kg) |
2017 |
15,400 |
1,140 |
2018 |
18,400 |
1,330 |
2019 |
14,000 |
1,100 |
2020 |
11,000 |
990 |
2021 |
495 |
989 |
PRTR emissions: Nasu Plant *Emissions only (excluding transfers)
FY |
Xylene (kg) |
1,2,4-Trimethylbenzene (kg) |
2017 |
43 |
11 |
2018 |
66 |
17 |
2019 |
51 |
12 |
2020 |
50 |
12 |
2021 |
49 |
13 |
Specific measures on biodiversity
Headquarters grounds certified as an Ota Ward Protected Forest
Technoport Kamata, the location of TOKYO KEIKI’s
Headquarters, is an office building block that was built as a
redevelopment of the site of our former headquarters and
plant. Construction was completed in September 1990. Two-thirds
of the vast grounds were turned into a tranquil green
space environment.
Now, more than 30 years after the completion of
construction, the trees planted at that time have grown,
turning the grounds into a conspicuous green oasis in
Kamata, a district with little verdure.
The area around our Headquarters, in particular, is
surrounded by a variety of trees, and Ota Ward has
designated the more than 2,000-m² green space around the
Headquarters building as a “Protected Forest.”
Ota Ward Protected Forest
Measures to prevent the death of cherry trees due to
an invasive insect
Several large cherry trees that are nearly 50 years old grow on the grounds
of the Sano Plant. Each year, they bloom stunningly, delighting the eyes of
many people who live in the area. In recent years, however, cherry trees
withering and dying due to Aromia bungii or the red-necked longhorn, an
invasive insect that has entered the area from neighboring prefectures, has
become a problem. We received contact that damage due to this insect
had also occurred at the Sano Industrial Park. We conducted an inspection
of the cherry trees on the grounds and discovered signs of damage caused
by the insect’s larvae feeding. Accordingly, we injected the trees with
larvicide and set up nets to capture adult insects. Going forward, we will
continue to carefully maintain these trees as a symbol of the Sano Plant.
Injecting a tree with larvicide
Capturing an adult insect
Installation of netting