Conclusion of power purchase agreement for solar power
TOKYO KEIKI PRECISION TECHNOLOGY (TPT), which
produces hydraulic equipment for Asia in Vietnam, made
the decision to switch approximately 30% of the power
used in its factory to solar power as an initiative to reduce
GHG emissions and concluded a power purchase
agreement (PPA) for solar power in March 2022. With this
agreement, TPT expects to reduce its GHG emissions by
approximately 400 tons annually.
This initiative is a first for our Group, and we will be
considering similar arrangements for other production sites.
Heat shield paint applied to the roof of Sano Plant
Due to climate change, in recent years, severe rainfall
occurs frequently in the Sano Plant area. Because
of the increased risk of such damage as roof leaks
resulting from the sudden increase in rainfall, we, at
Sano Plant, conducted maintenance and repainted
on the plant’s entire roof. As a result of using a heat
shield paint, which reflects infrared rays to control an
increase in the temperature of the roof, we confirmed an
energy conservation effect by reducing the load on air
conditioning equipment during the summer months.
Calculating Scope 3 greenhouse gas emissions
In order to understand supply chain GHG emissions across
all of our business activities and effectively reduce them, we
calculated the total emissions of all of our supply chains.
The table to the right provides a breakdown of our
Scope 3 emissions (indirect emissions other than a
company’s own from its supply chain).
Emissions from purchased goods and services
(category 1) were the greatest at 49.6% of the total,
followed by use of sold products (category 11) at 38.4%.
Going forward, we will continue to maintain an
awareness of, and promote reductions of, GHG emissions
across all of our supply chains.
Overview of Scope 3 CO2 emissions calculation (FY2021) 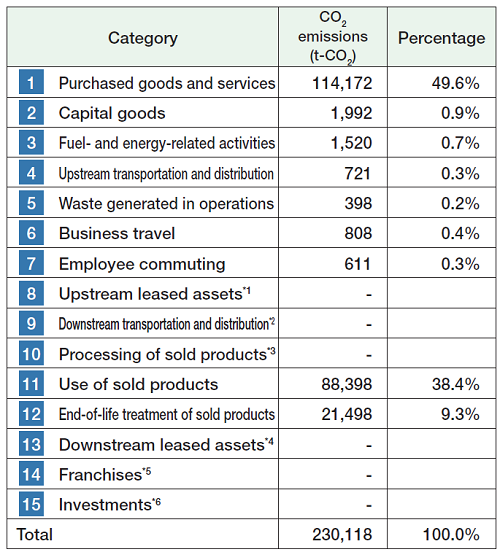
*1: Not applicable (emissions from leased assets included in Scope 1 and 2).
*2: Not applicable (finished product logistics outsourced and thus included in category 4).
*3: Not applicable (as TOKYO KEIKI’s products are finished products, they are not processed after sale).
*4: Not applicable (no relevant leased assets).
*5: Not applicable (no relevant franchises).
*6: Not applicable (no relevant investments).
Calculation method:
Based on standard guidelines from the Ministry of the
Environment and the Ministry of Economy, Trade and Industry concerning
the calculation of greenhouse gas emissions from supply chains.
Calculation period:
April 1, 2021–March 31, 2022
Calculation scope:
TOKYO KEIKI (non-consolidated)
MIRAI, a fuel cell vehicle, selected for President’s vehicle
MIRAI is a fuel cell vehicle (FCV) from Toyota that runs on
hydrogen fuel and emits zero GHGs. The Group’s TOKYO
KEIKI Vision 2030 identifies hydrogen and other energy
businesses as candidates for new growth drivers. Based
on this, the MIRAI was selected when updating the
President’s vehicle.