Through its business activities, the Group is working to reduce GHG
(greenhouse gas) emissions, which is an important issue of global scale. In
response to market and customer demands for environmental friendliness, we
will integrate the design, procurement, and manufacturing processes for our
products and services to provide added value, such as energy savings. In
addition, to reduce GHG emissions in Scope 1 and 2, we will pursue efficient
energy use by harnessing the creativity and ingenuity of all our employees.
|Environmental policies
-
We will evaluate the environmental impact of all our business activities and
the products we provide to our customers at during production, use, and
disposal, and strive to save resources and energy, reduce waste, and prevent
pollution.
-
We will establish and maintain a PDCA cycle by setting environmental
objectives and targets for these initiatives.
-
In addition to complying with environmental laws and regulations,
ordinances, industry codes of conduct, and agreements with local
communities, we will establish and maintain independent management standards
wherever possible.
-
We will establish an environmental management system in which all employees
participate, using audits and reviews to make improvements on an ongoing
basis.
-
We will provide education to all employees to improve their awareness of the
environment and the environmental management system, as well as asking our
affiliates and partner companies for their understanding and cooperation.
- These environmental policies shall be publicly disclosed.
Environmental policies in each district
Our Nasu, Yaita, and Sano plants have drawn up their own environmental
policies based on the company- wide policies, taking into account the
characteristics of the manufacturing they perform and consideration for
the surrounding environment. In order to put our basic philosophy into
practice, each district has formulated its own environmental policies and
is working actively to acquire various certifications, including ISO
14001.
ISO 14001 compliance status
Location |
Date acquired
|
Nasu Plant |
December 2005 |
Yaita Plant |
January 2007 |
Sano Plant |
April 2007 |
Tanuma Plant |
November 2006 |
|Environmental management structure
The Environment Committee is in charge of the Group’s environmental policy, and the
Environmental Management Subcommittee has been established beneath it.
The head of the Human Resources & General Affairs Department chairs
both committees, and the managers of the Nasu, Yaita, and Sano plants serve as committee members.
|Climate Change Initiatives
The TOKYO KEIKI Group is working to reduce GHG emissions and promote resource
and energy conservation to minimize the impact of our business on climate
change. At the same time, we are taking steps to mitigate the impact of future
climate change on the Group’s businesses.
Initiatives on TCFD recommendations
We announced our endorsement of the Task Force on Climate-related Financial Disclosures (TCFD) recommendations in August 2022. By comprehensively assessing the risks and opportunities that climate change poses to our business, we are incorporating adaptation and mitigation measures into our management strategies as we work to achieve TOKYO KEIKI Vision 2030.
If an initiative has a material impact on our business activities, we disclose it by such means as providing climate change-related financial information.
(1) Governance
To promote sustainability management, our Group
established the Sustainability Promotion Office and the
Sustainability Committee in June 2021. At the enter of
our Group, the Sustainability Promotion Office plans and
promotes measures involving sustainability management. The
Sustainability Committee is chaired by the Representative
Director, President & CEO and selects members from Internal
Directors and Executive Officers. It functions as a meeting
body that discusses and shares sustainability management-related policies and measures, and executes decisions
without delay across the Group. It also makes proposals
on key measures and issues progress reports to the
Management Conference and the Board of Directors.
The Sustainability Committee met six times in fiscal 2023.
It made proposals and reported on the progress of our
materiality initiatives and on our climate change scenario
analysis based on the TCFD recommendations. Their
proposals went to the Management Conference and Board of
Directors for deliberation before being adopted by the Group.
(2) Strategy
(2)-1. Scenario analysis based on TCFD recommendations
The TOKYO KEIKI Group recognizes climate change as a critical issue in the
sustainability management of the Group. For that reason, we created our own
scenarios based on the TCFD recommendations and referring to the 2°C and
4°C warming scenarios in the IPCC’s Sixth Assessment Report. Using
these scenarios, we evaluated the impact of a warmer climate in 2030, the
target year for achieving our mid- to long-term strategy. The table below
lays out our view of each scenario.
(2)-2. Assessment of risks and opportunities based on
scenario analysis and overview of initiatives
Based on the scenarios we created, we identify events
that could affect TOKYO KEIKI Group business activities
and measures to deal with them, and work on them in
materiality activities.
The table below gives an overview of initiatives in fiscal
2023. With respect to transition risks, we will continue our
initiatives to meet customer and market expectations. As
for physical risks, we are making preparations designed
to optimize the entire supply chain.
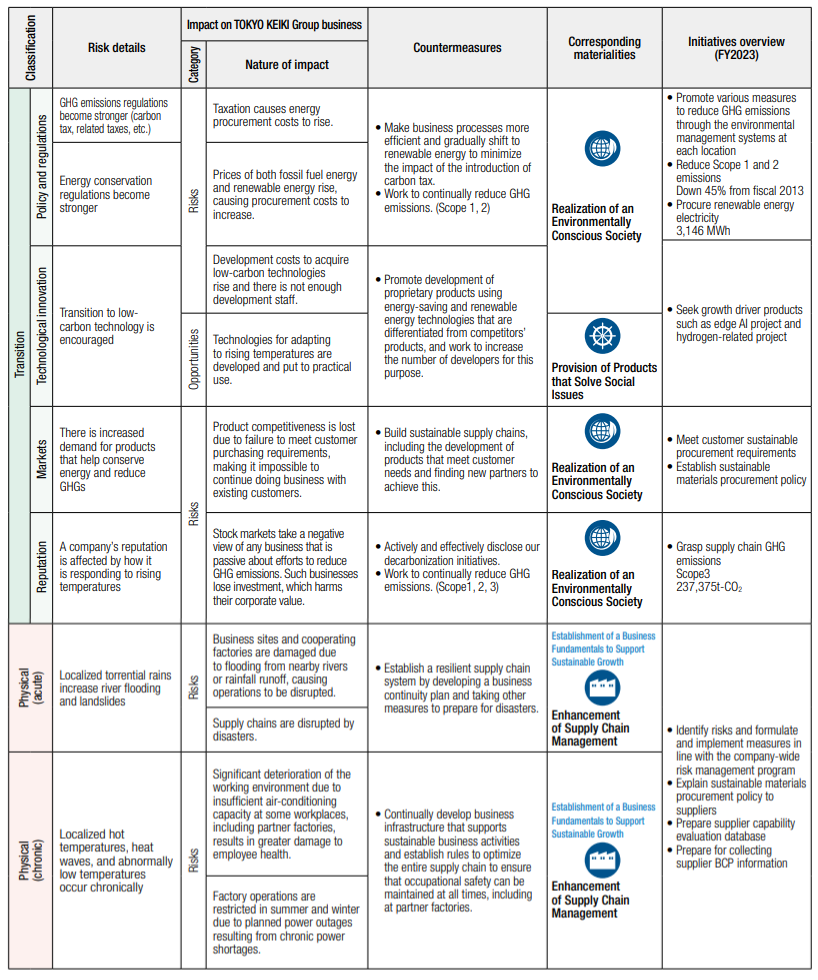
(3) Risk management
The TOKYO KEIKI Group manages risks in keeping with our risk management
system.* Following our Risk Management Rules, we classify risks as major
management risks or other risks and manage them accordingly. Risks that relate
to sustainability are written up for the Sustainability Committee’s
consideration by members of the Sustainability Promotion Office or
Sustainability Committee. The Sustainability Committee promptly discusses the
magnitude of the risks and how to deal with them. Its resolutions go to the
Management Conference and Board of Directors for deliberation and final
approval.
*See the risk management system diagram on p. 59.
(4) Indicators and targets
The Group set a target of reducing GHG emissions
within the Group by 37% in fiscal 2030 compared to
fiscal 2013. We are conducting activities to achieve this.
In fiscal 2023, our emissions were 7,050 t-CO2 (down 45% from fiscal 2013), which is already better than the
fiscal 2030 target. This is due to proactive initiatives on our part, such as the purchase of green power, which
began in fiscal 2022, and the signing of a PPA (power purchase agreement for solar power), which TOKYO
KEIKI PRECISION TECHNOLOGY CO., LTD. (TPT) began in fiscal 2023. Additionally, the CO2 emissions coefficient
for electric power utilities was significantly lowered since the previous fiscal year.
Moreover, the Nasu Plant’s solar power generation equipment began operating in fiscal 2024. We will continue
our work to keep emissions below the fiscal 2030 target.
The Nasu Plant has been working to reduce GHG emissions in several ways. For example, it has
systematically upgraded from fuel to electric air-conditioning and switched to green power for some of the
electricity it purchases.
Recently, it used idle land on its site to install a new facility to generate solar power for its own use. With solar
power providing about 6% of the electricity used at the Nasu Plant, it estimates it can reduce GHG emissions by
about 150 t-CO2 yearly. The Nasu Plant can use even the electricity generated on holidays without waste, as it has
a clean room that operates year-round.
Going forward, the Nasu Plant plans to implement an electric power monitoring system. By visualizing factory
electric power consumption, it will make effective GHG reductions.
Solar power generation facilities at Nasu Plant
❙ Initiatives for Environmental Management
In the manufacturing industry, it is our social responsibility to try to
minimize our impact on the environment when we choose materials and use energy
to make our products. By fulfilling this responsibility while engaging in
business activities, we will contribute to the realization of a sustainable
society.
|Initiatives to reduce waste
The TOKYO KEIKI Group aims to reduce the environmental impact of various types
of waste generated when manufacturing our products. Our Group-wide efforts to
reduce such waste are based on the 3Rs concept.
Waste is disposed of appropriately in accordance with laws and government
ordinances, as well as the regulations of the municipalities where our
factories and plants are located.
The use of equipment to reclaim wash oil and the evaporation and drying of wastewater from glass processing are helping to reduce the amount of
wastewater and waste oil we produce.
Amount of industrial waste produced in fiscal 2023 increased by 14 tons compared to the previous year due
to the large-scale disposal of deteriorated plastic pallets at the Yaita Plant and an increase in processing waste liquid
due to the breakdown of surface treatment equipment at the Sano Plant. We will continue to utilize environmental
management to promote reduction efforts.
We are now reusing some of our used products and parts (including
electronic parts) with the approval of our customers.
We hire contractors to take our scrap metal, waste oil, and waste paper, which are valuable recyclable materials,
and accordingly thoroughly separate our waste. The breakdown for these valuable recyclable materials for
fiscal 2023 was 344t of scrap metal, 16t of waste oil, and 53t of waste paper.
The Sano Plant alone accounts for about half of the company’s overall waste output, and roughly 60% of that
is water-soluble cutting fluid, wash oil, and other types of waste oil. To reduce the amount of these wastes, we
installed hydrocarbon-based wash oil recycling equipment in fiscal 2020. The equipment separates out about 10%
of the oil dissolved in the wash oil. The remaining 90% of the wash oil can be used as new, which reduces waste
and uses resources more effectively.
In fiscal 2023, the equipment recycled 7,877 liters of oil. Going forward, we will continue to recycle waste oil to
reduce our waste output.
|Measures for proper management of chemicals
Some chemical substances have harmful effects on the environment and human body. As such, it is companies’
social responsibility to manage them properly and to take the environment and occupational safety into account.
The Group is working to cut our emissions of chemicals by setting voluntary reduction targets.
Each of our factories is actively switching to alternative materials to hazardous chemicals.
-
Switched from dichloromethane to hydrocarbon-based
-
Switched to alternatives free from toluene and xylene
-
Switched to alternatives free from chlorine.
Reducing the amount of dichloromethane used for hydraulic products produced at the Sano Plant prior to
the coating process has been a challenge for a long time, but in January 2021 we succeeded in switching to a less
toxic hydrocarbon-based cleaning agent for all products except for some large products.
From fiscal 2023, we started using the agent for large products as well, enabling to eliminate the use of
dichloromethane and improve the working environment.
Pollutant Release and Transfer Register (PRTR) is a system to determine
the amount of hazardous Class 1-designated chemical substances discharged
from factories and report the results to the national government. The
government then compiles and publishes the data.
At the Sano Plant, we have no longer needed to submit reports to the government on dichloromethane emissions
since fiscal 2021 and on toluene emissions since 2020.
However, we will continue to monitor emissions of both substances.
PRTR emissions: Sano Plant *Emissions only (excluding
transfers)
FY
|
Dichloromethane (kg)
|
Toluene (kg)
|
2019 |
14,000
|
1,100
|
2020 |
11,000
|
986
|
2021 |
495
|
989
|
2022 |
743
|
927
|
2023 |
0 |
929 |
PRTR emissions: Nasu Plant *Emissions only (excluding
transfers)
FY
|
Xylene (kg)
|
1,2,4-Trimethylbenzene (kg)
|
2019 |
51
|
12
|
2020 |
50
|
12 |
2021 |
49
|
13 |
2022 |
13
|
11 |
2023 |
39 |
9 |
|Initiatives to protect biodiversity
Another critical social responsibility for our Headquarters, plants, business
locations, and other sites as we continue our business is to reduce the impact
on the surrounding environment and work to conserve it. The Group is committed
to protecting the environment site by site.
In May 2024, amidst the fresh greenery of spring, members of TOKYO KEIKI’s Marine Systems Company
joined the Spring UMIGOMI Zero Week 2024 activities organized by the Japan Ship Machinery and Equipment
Association (JSMEA). These activities are part of a joint project of The Nippon Foundation and the Ministry of
the Environment (with support from the Ministry of Land,
Infrastructure, Transport and Tourism) to combat marine trash. TOKYO KEIKI endorses the aims of the project.
At this event, a total of 31 people, together with
members of other endorsing companies, collected the
equivalent of 20 garbage bags of trash at Tatsumi-no-Mori Seaside Park in Koto Ward on Tokyo Bay.
Marine plastic trash is a global problem, and about 80% flows into the ocean from the land. This is because trash
tossed along roadsides and in tourist areas is carried by wind and rain into rivers and waterways, ultimately reaching the sea.
Although our efforts are small, we will continue working as a company to contribute to society and protect the natural environment.